The primary difference between low carbon ferrochrome (LC FeCr) and high carbon ferrochrome (HC FeCr) lies in their carbon content and the specific applications for which they are used. Here are the key distinctions:
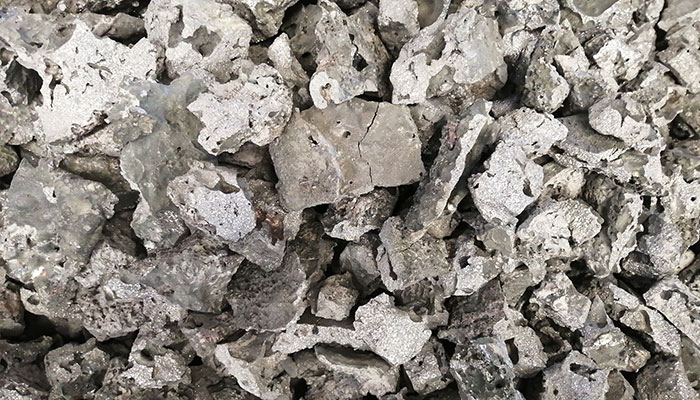
Low Carbon Ferrochrome (LC FeCr): LC FeCr has a significantly lower carbon content, typically kept below 0.10%, and often even lower. The controlled low carbon levels are crucial for applications where maintaining corrosion resistance, especially in stainless steel, is a primary concern.
High Carbon Ferrochrome (HC FeCr): HC FeCr has a higher carbon content, typically ranging from 4% to 8%. This higher carbon content makes HC FeCr more suitable for applications where increased hardness and strength are desired, such as in certain alloy steel and tool steel production.
Low Carbon Ferrochrome (LC FeCr): LC FeCr is primarily used in the production of stainless steel, where low carbon levels are critical for maintaining corrosion resistance. It is also used in other specialty steels and alloys where controlled carbon content is important for specific properties.
High Carbon Ferrochrome (HC FeCr): HC FeCr is commonly used in alloy and tool steel production, where the higher carbon content contributes to increased hardness and strength. It is also used as a charge material in the production of stainless steel.
Low Carbon Ferrochrome (LC FeCr): LC FeCr is an essential alloying agent in stainless steel production. The low carbon content helps prevent the formation of chromium carbides, which could otherwise reduce the corrosion resistance of stainless steel.
High Carbon Ferrochrome (HC FeCr): While HC FeCr is not the primary choice for stainless steel production due to its higher carbon content, it can be used as a charge material in some stainless steel manufacturing processes.
Low Carbon Ferrochrome (LC FeCr): LC FeCr is favored in applications where corrosion resistance is critical, such as in the manufacturing of kitchen appliances, cutlery, and components for chemical processing industries.
High Carbon Ferrochrome (HC FeCr): HC FeCr finds applications in industries where increased hardness and wear resistance are essential, such as in the production of certain alloy steels used for tools and machinery.
In summary, the choice between low carbon ferrochrome and high carbon ferrochrome is driven by the specific properties required in the end product. LC FeCr is favored for applications where corrosion resistance is crucial, such as in stainless steel, while HC FeCr is used when higher hardness and strength are desired, as in certain alloy and tool steel applications.