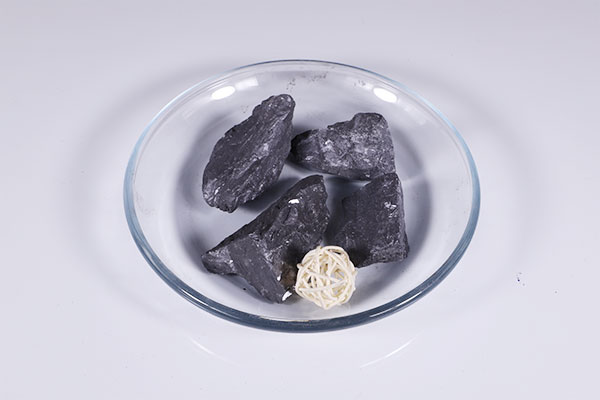
Calcium Silicon
What Is Calcium Silicon
Calcium Silicon is an alloy composed of two elements: silicon and calcium. It has a calcium content of 22 to 35% and a silicon content of 60 to 65%. It also contains impurities such as iron, aluminum, carbon, sulfur and phosphorus in varying amounts.
Calcium silicon is available in various forms, including lumps, granules, and as a cored wire for more controlled and efficient alloying.
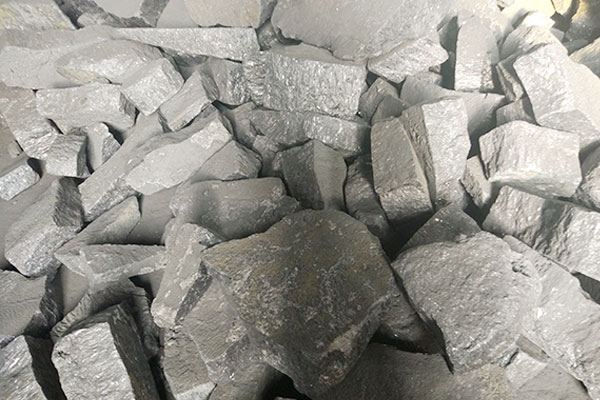
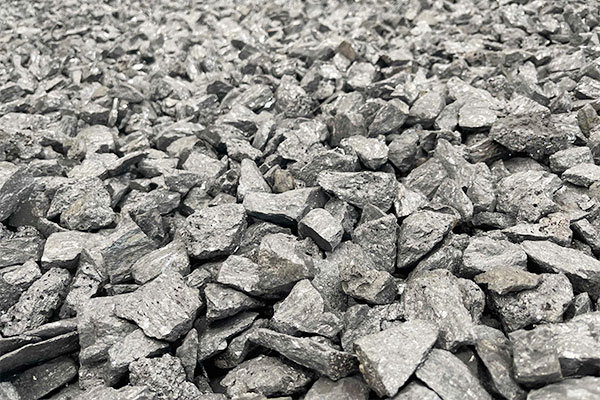
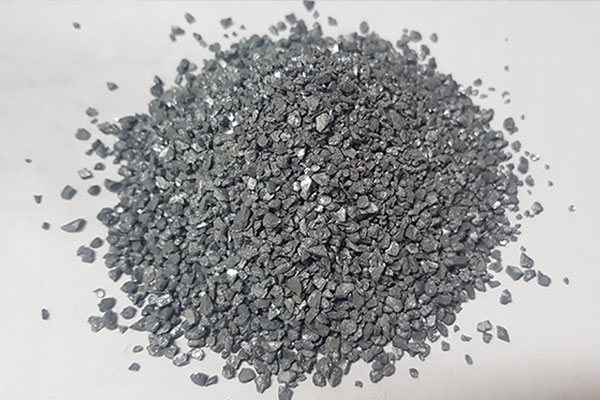
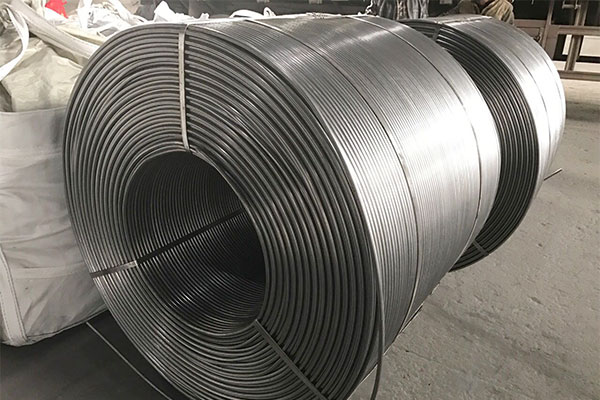
As far as calcium silicon alloy is concerned, 80% of the current silicon calcium alloy is added to the steel in the form of silicon calcium cored wire. CaSi Alloy in the form of cored wire feed into the steel, the utilization rate of calcium can reach more than 12%, which is 1.5 times that of silicon calcium block when adding liquid steel.
Calcium Silicon Specifications
Specification | Calcium Silicon Chemical Component | |||||
Ca | Si | Al | C | P | S | |
>= | <= | |||||
Ca30Si60 | 30 | 55-65 | 0.3 | 0.1 | 0.035 | 0.02 |
Ca28Si55 | 28 | 55-60 | 0.3 | 0.1 | 0.04 | 0.02 |
About Calcium Silicon Packing And Delivery
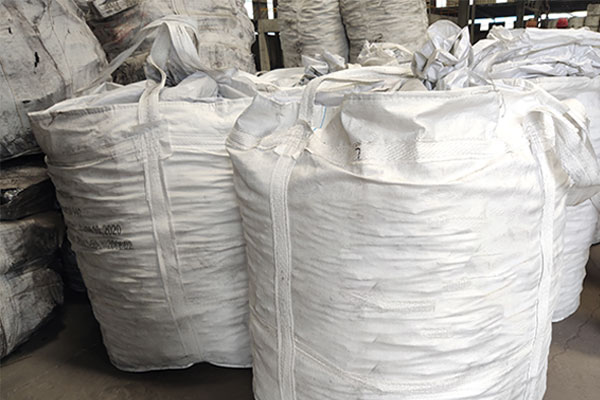
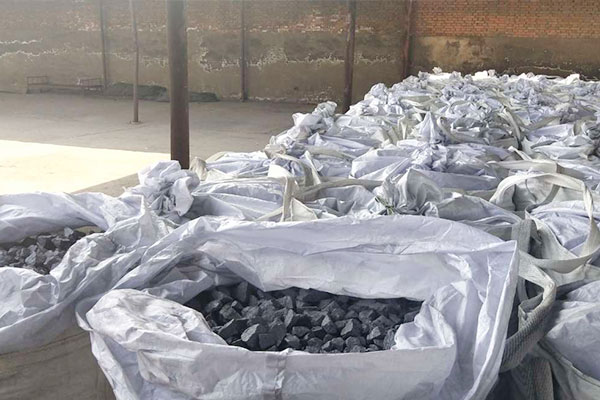
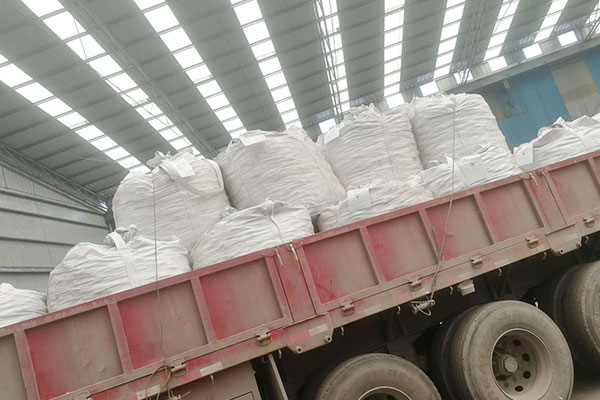
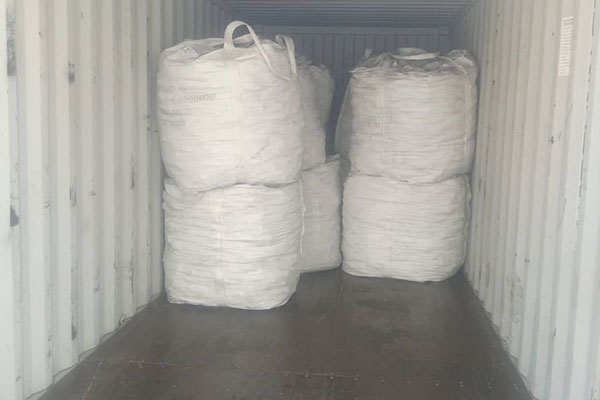
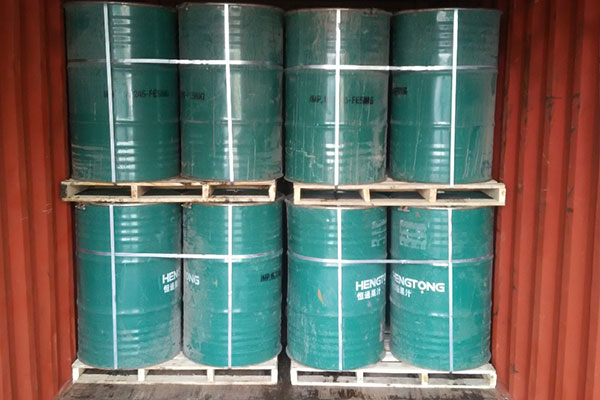
How To Produce Calcium Silicon
There are three kinds of production methods of silicon calcium alloy: mixed feeding method, layered feeding method and two-step method.
In China, the mixed feeding method and layered feeding method are generally used to produce calcium silicon Alloy. Germany, France and other countries use the two-step process to produce silicon calcium .
Characteristics of Calcium Silicon
Properties Of Calcium Silicon
Calcium silicon (CaSi) finds various applications in the steelmaking and metallurgical industries due to its deoxidizing, desulfurizing, and alloying properties.
What Is The Use Of Calcium Silicon
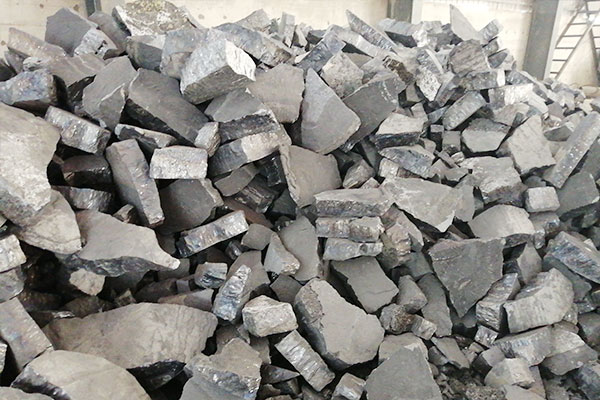